Le viaduc de
Millau, France - Le pont le plus haut du monde.
En juin de l’année dernière, la société
Enerpac (Technologie Hydraulique) remporta le contrat pour
la fourniture du système hydraulique qui sera utilisé pour
soulever les palées provisoires et pousser les tabliers lors
de la construction du viaduc de Millau. Aujourd’hui les
travaux battent leur plein et, pendant que vous lisez ceci,
se construit le pont le plus haut du monde.
Les tabliers
Les études pour la construction du viaduc de Millau
débutèrent en 1988 avec pour objectif de mettre fin à
l'engorgement de la A75, l'autoroute reliant Paris à
Barcelone. Entre plusieurs trajets possibles, le CETE
(Centre d'Etude des Techniques d'Équipement) choisit le 28
juin 1989 un trajet médian passant à l'est de Millau et
franchissant le Tarn. Ce qui impliquait la construction d'un
long viaduc d'une très grande hauteur, lequel devait
survoler la vallée du Tarn sans y descendre, évitant ainsi
le percement d'un tunnel. Option choisie en 1991 car
affectant à peine l'environnement et offrant une meilleure
sécurité. Les études détaillées eurent lieu en 1993, et cinq
bureaux d'architectes participèrent au concours lancé en
1994. En 1996 fut choisi le projet émanant d'un groupe
d'ingénierie français se composant de Sogelerg, EEG, SERF et
Foster.
Du projet à la réalisation
Plan.
Le projet Foster impressionnait par l’esthétique et la
taille de l’ouvrage. Sa construction n’était pas
particulièrement facile si l’on voulait éviter des coûts
prohibitifs. Soutenu par deux culées et sept piles, le
viaduc survole la vallée du Tarn sur une distance de 2 460
mètres à une hauteur centrale de 245 mètres. 204 mètres
séparent les culées de la première et de la dernière pile,
et les travées font 342 mètre entre les autres piles dont
les hauteurs varient de 70 mètres pour la première, à 340
mètres pour la troisième.
L’ouvrage est haubané et comporte des éléments verticaux en
béton creux en forme de diapason lesquels supportent les
deux chaussées à partir du centre. Les chaussées ont une
largeur totale de 27,35 mètres, et permettent l’installation
de trois voies de circulation dans chaque direction (dont
deux seulement seront mises en service au début de l’
exploitation) et d’un accotement sur les deux côtés.
Pour les conducteurs, le viaduc se présente avec une légère
pente (3,035 % du nord vers le sud) et une faible courbe
(rayon 20 000 mètres). Au centre, il culmine à 270 mètres
au-dessus du niveau du sol, et la pile centrale avec son
haubanage dépasse les 340 mètres, soit 14 % de plus que de
la Tour Eiffel.
Il fallut choisir entre deux types de tabliers, béton ou
acier. Le choix se porta sur l’acier, celui-ci permettant
une construction non seulement plus mince, donc plus
esthétique (un tablier en béton demandait une épaisseur de
4,6 mètres), mais également plus sûre et cela aussi bien
pendant la pé riode de construction qu’après la mise en
service.
27 000 mètres cubes de béton, 19 000 tonnes d’armatures pour
béton, et 5 000 tonnes d’acier pour les câbles et les
recouvrements furent nécessaires pour la construction. Pour
les piles, le choix se porta sur un béton haute performance
B-60 et sur l’utilisation de coffrages métalliques du type
self-climbing de différentes formes.
Le 9 juillet 1996, après le choix de la configuration finale
des travaux, il fallut déterminer qui les exécuterait et
comment. Plusieurs entreprises soumirent des offres, et le
Département Franç ais des Transports et Travaux Publics
porta son choix sur le Groupe Eiffage TP (3ième en taille en
France, 5ième en Europe), lequel créa une nouvelle société
pour l’exécution de ces travaux, la Compagnie Eiffage du
viaduc de Millau. En échange du financement des travaux,
coûts estimés (au début des opérations) à 300 000 000 € plus
20 000 000 € pour un futur poste de péage situé 6 kilomètres
plus au nord, cette compagnie obtint une concession
d’exploitation d’une durée de 75 ans.
La construction est conçue pour résister aux secousses
sismiques et aux conditions mété orologiques les plus
extrêmes, son utilisation est garantie sans problèmes pour
une durée minimale de 120 années. Du point de vue
construction, le tablier avec sa masse de 36 000 tonnes,
constitue le problème le plus important. Il sera poussé à
partir des deux extrémités du viaduc. Les éléments du
tablier seront fabriqués sur les sites de Eiffel à
Lauterbourg et Fos-sur-Mer, et un ensemble de 64 vérins
hydrauliques sera utilisé pour effectuer les poussées. Les
translations, sur une longueur de 342 mètres, doivent se
faire sur la longueur des six travées centrales et
nécessitent l’installation de cinq palées provisoires, à la
construction desquelles participe la division espagnole
d’Enerpac.
Les palées provisoires sont soulevées à l’aide d’un
système hydraulique
Entre les piles, sept palées provisoires seront nécessaires
pour lancer le tablier.
Lors de la conception du viaduc de Millau, Eiffel, une
filiale du groupe Eiffage et spécialisée dans la
construction métallique, a estimé que pour assurer la
translation des tabliers pendant la construction, il fallait
installer sept palées provisoires entre les piles. Deux de
ces palées provisoires, aux extrémités de l’ouvrage,
s’installent directement à l’aide d’une grue car leur
hauteur ne fait que 20 mètres et 12 mètres. Par contre la
hauteur des cinq palées provisoires restantes varie de 87,5
mètres à 163,7 mètres. Pour celles-ci, un système de levage
télescopique a été conçu et l’exécution de sa partie
hydraulique a été confiée au bureau régional Enerpac en
Espagne.
Dès qu’une palée provisoire a été élevée, le système de
levage télescopique comprenant l’équipement hydraulique est
démonté et déplacé vers l’endroit où doit s’installer la
palée suivante.
Système télescopique pour le levage des éléments des
palées provisoires
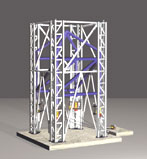 |
Le système de levage télescopique se compose de deux
parties:
- La première consiste en une construction
métallique de forme cubique dont la base, qui
contient tout le système, fait 12 mètres de
côté; elle est équipée de crémaillères graduées
en mètres à partir des pieds de la construction.
- La seconde comprend les vérins et le système
de commande hydraulique qui forment le mécanisme
de levage. Les vérins hydrauliques sont
installés aux quatre pieds de la construction,
ancrés à des supports reliés aux crémaillères et
qui permettent, grâce à l'insertion successive
de cales de verrouillage dans les crémaillères,
le déplacement vertical d'un élément de la palée
provisoire et de l'équipement hydraulique,
guidés par les colonnes du système de levage.
|
Pas de levage égal à 1000
mm
Système hydraulique.
Le fonctionnement est simple; les supports des vérins sont
verrouillés dans les crémaillè res à l’ aide de cales,
l’élément de la palée provisoire étant libre. Les
opérateurs, à l’ aide du dispositif de commande, comprenant
un logiciel détaillé et incorporant toutes les options de
sécurité nécessaires, commencent par mettre sous pression
les vérins dont les tiges poussent l’élément de la palée
vers le haut. De cette façon, celui-ci est levé à la hauteur
de la perforation suivante dans la cré maillère. Les vérins
ont une course de 1100 mm et les crémaillères sont munies de
crans tous les 1000 mm, reste donc une plage de 100 mm pour
compenser d’éventuelles irrégularités. Chaque vérin
hydraulique possède sa propre commande avec possibilité de
verrouillage immédiat, et divers capteurs renseignant sur
les modifications des conditions extérieures (vent,
température, etc.) qui pourraient conduire à un ajustement
dans l’opération de levage des éléments de la palée
provisoire.
Chaque vérin de levage opère de façon indépendante. Dès que
la hauteur désirée est atteinte, l’élément de la palée est
verrouillé en place à l’aide de cales et les cales support
de vérin sont débloquées. Les tiges de piston sont rentrées
et les vérins hydrauliques sont élevés avec leurs supports
vers la perforation dans la crémaillère située immédiatement
au-dessus, où ils sont à nouveau verrouillés à l’aide de
cales. De cette façon, l’élément de la palée et le
dispositif de levage hydraulique sont élevés de 1 mètre, ce
processus se répétant jusqu’à ce que le premier élément
dépasse la structure du système de levage. Il est ensuite
verrouillé à sa base. Quand le dispositif hydraulique a
rempli sa fonction, il est descendu jusqu’au sol à l’aide
d’une grue car à présent son poids est moindre. Un second
élément de la palée prend alors place dans le système de
levage et est levé de la même façon à l’aide du dispositif
hydraulique, et ainsi de suite jusqu’à ce que la nouvelle
palée provisoire atteigne la hauteur nécessaire pour
supporter la partie de tablier qui sera poussée en place.
Commande du processus
Système
de levage hydraulique; précision du levage 3 mm
Le système a été conçu pour empêcher, à n’importe quel
moment, une déviation en hauteur de plus de 3 mm et une
différence de charge dé passant au maximum 5 % entre chacun
des vérins.
Chaque vérin est alimenté par sa propre pompe hydraulique de
façon à ce que, si nécessaire, il puisse être commandé
individuellement, à condition que la procé dure complète de
la demande pour le faire, ainsi que l’autorisation, passent
par la centrale de commande de l’application.
Les opérateurs, installés à chaque extrémité de la
structure, travaillent à l’aide de commandes reliées à la
centrale et qui leur permettent de valider l’insertion et le
retrait des cales pendant toute la durée du processus. Dès
réception du signal, la personne en charge de la centrale de
commande donne l’ordre autorisant la poursuite du processus.
L’ensemble est également muni de systèmes permettant la
surveillance du niveau et de la tempé rature de l’huile et
d’alarmes qui arrêtent la translation en cas d’imprévus
comme chute de pression, rupture de flexible, etc.
Spécifications techniques
La partie hydraulique du système de levage comprend quatre
vérins, chacun alimenté par sa pompe propre, raccordés à un
tableau de commande central. Chaque assemblage a une
capacité de poussée égale à 511 tonnes, soit une capacité de
poussée totale de maximum 2044 tonnes. Comme il n’est
normalement pas prévu de dépasser la poussé e de 420 tonnes
requise durant les cycles de travail, le système possède
donc une géné reuse marge de sécurité. La pression nominale
est de 700 bars et, comme mentionné plus haut, la course des
vérins égale 1100 mm. Une surcharge de 675 tonnes, vérin en
extension, et de 1500 tonnes, vérin rétracté, est
acceptable.
L’ensemble commande centrale (câblage, tableau de commande,
écran) est protégé contre les intempéries et les
perturbations électromagnétiques, et contre les impacts
pouvant survenir lors de l’installation ou pendant le
travail.
Enerpac, filiale du groupe Actuant basé aux Etats-Unis,
possède une longue expérience dans le domaine de la
fabrication de divers types d’équipements et de systèmes
hydrauliques haute pression pour l’industrie et la
construction, à l’origine elle se fit connaître par la
fabrication d’ amortisseurs destinés à la légendaire Ford T. |